Metal Fabrication Boise Idaho is an industry much like the printing business. During the day, people come in contact with products from both industries that seem ubiquitous—think doors and door latches, hangers, screws and nails, and more.
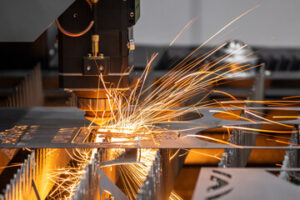
One of the biggest challenges for the metal fabrication industry is finding skilled workers. Many companies are taking steps to address this issue, from partnering with local schools to offering apprenticeships.
Whether you’re looking for the right metal fabrication shop or working on your own project, it helps to know the ins and outs of the design process. You need to understand the fundamentals of the metal fabrication industry, including what materials are available, how to cut and weld them, and how finishing options like powder coating or plating can affect the final look and durability of your product or component.
Many metal fabrication shops offer a variety of services in-house, from cutting to welding and machining to assembly and finishing. Ask about which services each company handles, and how much of their work they outsource to other companies. This will give you a better idea of how experienced and diversified they are, which may affect the quality of their work.
The skilled labor shortage is a challenge that continues to plague the industry, which can result in longer lead times and higher costs for customers. To combat this, metal fabrication companies are partnering with schools and community colleges to provide training programs. They’re also focusing on improving efficiency and implementing new technology to streamline the process and reduce waste.
Another significant trend is the rise of 3-D printing and other additive technologies, which can create parts in a more cost-effective way than traditional manufacturing methods. Metal fabrication companies must continue to innovate to stay competitive and keep up with these changes. They’re developing more automated equipment and tools that can make the same repetitive tasks that skilled human workers used to do faster, with fewer errors and less wasted material. This will allow them to offer lower costs for low- and high-volume orders. They’re also finding ways to reuse and recycle water, reducing their overall environmental impact.
Cutting
The cutting process in metal fabrication involves slicing through sheets of metal with various types of machines. Shearing is a common method used to cut straight lines on flat metal stock, necessary for sizing sheets before they undergo other fabrication processes. Other cutting techniques include punching, stamping, and milling. Milling uses a rotating tool to remove excess metal from the workpiece. Other cutting tools include abrasive wheels, a drill, and grinding.
Rolling is another popular fabrication technique. It involves passing metal through a series of rollers to reduce or balance its thickness, as well as shape it by plastically deforming the material. This is important for forming the curves and bends in fabricated parts and structures. Standard metal fabrication parts like discs, stampings, wheel rims, and tubes are often rolled, as are many other products like wire baskets and ductwork.
For more precise and accurate cuts, metal fabricators use computer numeric control (CNC) machines. These are highly flexible and can follow patterns, making them a key part of modern automation in the industry. However, they still require skilled workers to program, operate and maintain them.
In addition, some parts and pieces may be more complex than others, requiring a more intricate design or a specific dimensional requirement. For these instances, metal fabrication companies use CAD programs to create 3-D renderings and 2-D schematics that help customers understand what their finished product will look like.
Ultimately, the quality of a fabricated metal part depends on how well the product is designed. This is why it is essential to partner with a reputable metal fabrication company that has a team of experienced designers and engineers on staff. These professionals can ensure the final product meets your exact specifications.
Forming
The forming step in metal fabrication takes the raw materials that were cut into smaller pieces and shapes them into the final product. Depending on the type of product, this can include steps like shearing and punching. It can also involve bending and stretching metal to make it more compact. It’s often necessary to weld parts together at this stage, although adhesives are sometimes used for lightweight components.
One of the biggest challenges for the industry is finding and training skilled workers. Many experienced fabricators are retiring and there aren’t enough new people to replace them. The shortage can affect everything from welding to operating complex machinery. Many companies are trying to address the issue by partnering with local schools and community colleges to create training programs. Some are also offering apprenticeships and on-the-job training.
Another challenge is the volatility of raw material prices. These can spike for a variety of reasons, including global demand, supply chain disruptions, and changes in trade policies. This can make it difficult for metal fabricators to stay profitable, especially if they’re locked into long-term contracts with suppliers. Some companies are hedging against price fluctuations, while others focus on improving efficiency and reducing waste to offset costs.
Automation is also making its way into the metal fabrication industry. Robots can take on tasks that would otherwise require human welders and do them more quickly and accurately. They’re also helping to reduce energy costs and waste by lowering usage of harmful chemicals. Many companies are also using recycled metal scraps and sourcing their power from cleaner sources. These steps help to produce more sustainable products and increase customer satisfaction.
Assembly
From the tiny machine part inside a mechanical watch to the massive steel beams that form the skeleton of a skyscraper, metal fabrication products are in widespread use throughout the world. These custom-designed and manufactured pieces are known as components, and they serve specific functions within extensive systems or structures. From a business point of view, the industry has grown steadily, even during the COVID-19 pandemic, as manufacturers continue to produce products that are in high demand across multiple industries.
The assembly and integration stage involves putting the individual fabricated parts together to transform them into a completed product or system. Welding is the most common method of joining these parts, and it offers strength and reliability. However, it is not the only option, as some fabricators use fastening methods like bolts, screws, and rivets to join components. Other options include adhesive bonding, which uses specialized glues to join metal components, and is useful in cases where welding is not possible or desirable.
For welded assemblies, quality control is particularly important because the process can cause distortion and warping. To minimize these effects, manufacturers must prepare the materials before welding by using jigs and fixtures to hold them in place, and by choosing appropriate welding techniques and parameters.
The other main assembly technique used in metal fabrication is forming. This involves bending or folding metal sheets into a desired shape, and can be accomplished with tools such as hammers (both manual and powered), coining machines called shears, and press brakes that either coin or bend metal sheet stock into the desired shape. Examples of fabricated formed metal parts are brackets, which are often used in enclosure shelves, and panels, which are commonly seen in structural steel projects, such as the new Tappan Zee Bridge that EVS Metal recently worked on.
Finishing
There are a number of different finishing techniques, and choosing the right one can make or break a fabrication. It can affect how it looks, how long it lasts and, inevitably, its cost. That’s why finishing is one of the most important steps in metal fabrication.
During the design phase, engineers create detailed drawings or models that serve as blueprints during production. They consider strength requirements, tolerances and other factors to determine which materials and production techniques should be used.
Once the prototype is complete, it goes through a series of processes that transform it into its final form. This can involve bending, stretching and other deformations to achieve the desired shape. Welding may also be required at this stage if parts are being joined permanently.
In addition, many fabricated metal pieces require special treatments to protect them from corrosion and enhance their appearance. Examples of these include anodizing and passivating. Anodizing creates an oxide layer on the surface of aluminum, which protects it from oxidation and improves its durability. Passivating removes iron particles from the surface of stainless steel, which can cause unsightly corrosion.
Like other manufacturing industries, metal fabrication is subject to price fluctuations for raw materials. Spikes in prices can squeeze fabricators’ profit margins and lead to higher costs for customers. To combat this, some companies use financial instruments to hedge against price changes and invest in training programs that provide skilled workers.
Regardless of whether they work with small, medium or large industrial manufacturers, metal fabricators need access to advanced technology and high-quality engineering solutions that will enable them to stay competitive and grow their business. That’s why it’s so important to find a partner with a strong track record and expertise in the latest manufacturing technologies and techniques.